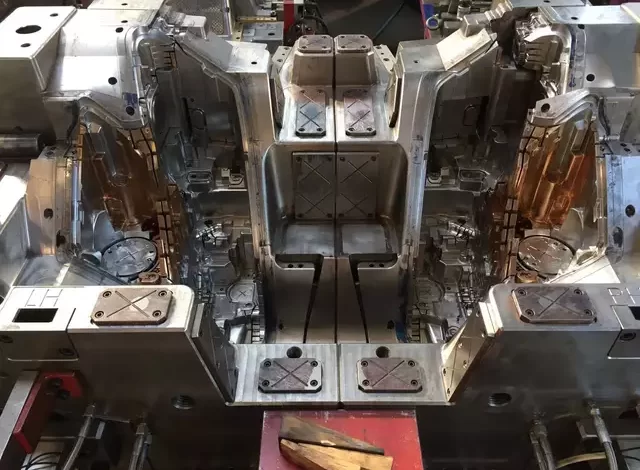
Injection molding is a manufacturing process that creates plastic parts by injecting heated liquid resin into a mold. It’s used to make many products, including toys, automotive products and food containers. While injection molds have application for both large and small projects, they are especially useful for mass-producing plastic parts quickly and at low cost. Here are the top five benefits of using injection molds:
Injection molds are a fast way to mass produce plastic parts. Injection molding is a low cost way for manufacturing high volumes of plastic parts. New products can be designed and manufactured at a quick pace, which can be beneficial in the marketplace. In many cases, manufacturing with injection molding will result in fewer defects than other processes.
The process begins with the injection of a polymer into a heated barrel, which melts the material and forces it into the cavity of the mold. The injection ram then moves forward, pushing the molten plastic into the mold cavity. When it reaches the end of its stroke, it returns to its starting position and repeats this cycle until all of the material has been injected into the mold. The part itself is ejected from this system once it cools down and solidifies.

1.A fast way to mass produce Injection Molding parts
Injection molding is a fast, cost-effective way to mass produce plastic parts. The process requires only an injection molding machine, raw materials and some kind of cavity (the shape of the part). It’s a high-volume production method that allows you to make hundreds or thousands of identical parts in a single run.
This is especially useful when you need large quantities of certain types of parts. For example, if you’re making smartphone cases and want to use different colors for each model but don’t want to do any handwork or painting yourself (and don’t mind paying extra), there are companies that will create molds for you based on your design so all they need is your artwork file.
Those molds are made and approved by quality assurance teams at these companies. Those molds can be used indefinitely with very little upkeep required except replacing any broken pieces from time to time. It wouldn’t happen unless someone dropped one on their toe!
2.A low cost way for manufacturing high volumes of Injection Molding parts
Injection molding has been used in the manufacturing of plastic products for many years. The process can be used to create a wide variety of products from medical devices to toys, from automotive parts to plumbing fixtures, and from electronic components to food containers.
The process is also used for creating plastic parts for a wide range of consumer products. Injection molding has many advantages over other types of manufacturing processes, such as casting and machining. In addition to the lower cost, it can produce high quality parts with intricate details and tight tolerances.
3.New products can be designed and manufactured at a quick pace
The process of developing new products, or creating new designs for existing products, is known as product development. The concept of product development is not new; it has been around for centuries. However, the application of this concept has changed dramatically over time, due to improvements in technology and other factors.
New products can be designed and manufactured at a quick pace, thanks to advancements in technology. For example, 3D printers can be used to quickly produce prototypes that can then be tested and modified before being mass produced (see How 3D Printing Works).
In addition to advances in technology, companies are also employing different methods of research and development (R&D), which allow them to develop new products more quickly than ever before. Many companies now use agile software development methods that involve frequent releases of software updates rather than waiting until a complete version is ready (see Agile Software Development).
4.Injection molded parts can be made uniform and with high tolerances
Injection molded parts can be made uniform and with high tolerances. This makes them ideal for applications where there are tight tolerances and where dimensional consistency is important. For example: automotive parts, medical devices and consumer electronics.
Injection molds also allow for very small features to be produced in plastics that would be difficult or impossible to produce by other methods. In addition, injection molds allow for multiple parts to be produced simultaneously as they are all molded from one single mold cavity; this enables a high degree of automation which helps reduce labor costs while increasing productivity.
5.Ability to Use Recycled Plastics
Recycled plastics are a popular choice for many manufacturing applications. The ability to use recycled plastics is a benefit for a number of reasons.
Recycled plastics can be used in place of virgin materials. This helps save energy and reduces the need for mining operations.
Recycled plastic products are often less expensive than their virgin counterparts. This is because they don’t require as much processing time or energy, which lowers production costs.
The ability to use recycled plastics also reduces the need for virgin materials, which means less demand on resources like oil and coal. This also helps reduce pollution caused by mining operations and other types of industrial activity that rely on non-renewable resources.
Recycled plastics are available in a wide range of qualities, sizes, colors and shapes in virtually any application imaginable. These qualities make them extremely versatile and cost-effective for manufacturers, who can take advantage of this versatility without having to sacrifice quality or performance in their products
6.Minimal waste production
Injection molding produces very little scrap material compared with other plastic manufacturing processes because there is little finishing or trimming required. You can also avoid secondary operations like polishing and painting that often produce scrap material. This is especially important for companies that want to avoid having to dispose of waste and recycle as much material as possible. This is also important for companies that are trying to reduce their carbon footprint.
Why 3D printing?
3D printing is a process of making three dimensional solid objects from a digital file. 3D printing has the potential to revolutionize manufacturing and the health care industry.
Benefits of 3D Printing:
1. Cost Effective:
The cost of using 3D printers for manufacturing small batches of products is much cheaper than producing large quantities on traditional assembly lines. This will give companies the opportunity to create low-volume production runs without huge investments in tooling, equipment and labor costs. It can also reduce or eliminate the need for outsourcing product development or prototyping to overseas manufacturers. It can be expensive and time-consuming.
2. Customization:
3D printing allows you to customize products according to your needs and specifications, allowing for real-time customization of products for end users or customers without having to go through multiple stages of design and development processes.
This helps reduce lead times and increase efficiency by eliminating unnecessary steps in the design and development process . And it will also reduce waste by not producing items that have no need by customers or end users.”
Takeaway
Injection molding is an extremely versatile process. If you are able to make a part by CNC machining or through another additive manufacturing method, that opens up the door to all sorts of possibilities. You can also leverage injection molding in other ways, such as when your part has complex geometry that would not be possible with other methods and materials.